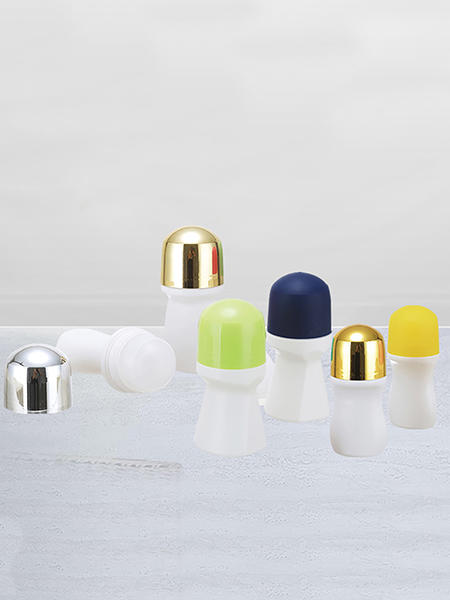
To further enhance the bottle’s sealing performance, many PP roll-on bottles incorporate an inner liner, typically made from materials such as foil, foam, or rubber. This liner forms a secondary barrier between the bottle’s contents and the outer environment. The liner is positioned between the bottle’s neck and the cap, ensuring a tight seal when the cap is closed. This seal is particularly beneficial in preventing liquid from escaping during transit or when the bottle is tilted. The inner liner effectively seals the bottle, even if external pressure or temperature fluctuations create slight changes in internal volume, reducing the risk of leakage.
The threaded cap design is one of the most common and reliable sealing mechanisms in PP roll-on bottles. The cap features threads that tightly match the bottle’s neck, ensuring that the cap is securely screwed on. When properly sealed, the threaded closure prevents accidental loosening, even during rough handling, shipment, or storage. The threaded design offers precise engagement, allowing the cap to sit firmly in place without wobbling. This, combined with the inner liner, provides a robust seal that is resistant to both external and internal forces that could otherwise cause leakage.
The roller ball mechanism, which is a distinctive feature of the roll-on bottle design, plays a vital role in the sealing process. The ball is typically constructed from durable materials, such as stainless steel or ceramic, and is designed to fit snugly into a socket at the top of the bottle. When the bottle is not in use, the ball remains securely seated, with a sealing ring or gasket at the base of the ball. This sealing ring ensures that no liquid can escape through the roller ball socket, even when the bottle is tilted or shaken. The smooth ball mechanism also facilitates an even, controlled release of the product during application, without any spillage or leakage, contributing to the bottle's overall leak-proof performance.
Some PP roll-on bottles are designed with advanced sealing technologies, including caps equipped with double-action sealing systems. In these designs, an additional sealing ring or gasket is integrated into the interior of the cap. This extra layer of sealing material compresses tightly against the neck of the bottle once the cap is screwed or pushed in place, providing a more robust seal. The double-action design prevents any potential leaks by ensuring that even the smallest gap between the cap and bottle is sealed. The combination of the primary threaded closure and this additional compression seal enhances the bottle’s ability to resist leaks, especially when subjected to external pressures or physical movement.
Some high-performance PP roll-on bottles are equipped with specialized air vent or valve systems that regulate internal pressure fluctuations. Changes in temperature or rapid movements can cause a buildup of internal pressure within the bottle, which could lead to leakage or product spillage. To mitigate this, air venting systems are incorporated to allow controlled release of pressure, preventing the bottle from deforming or expelling product through weak spots. These air vents are strategically placed within the cap or the body of the bottle to release pressure in a controlled manner, ensuring that the liquid remains sealed inside the bottle. This feature is especially important for products containing volatile or sensitive ingredients, as it maintains the quality of the product while preventing leakage.
Leave a Reply
Your email address will not be published.Required fields are marked