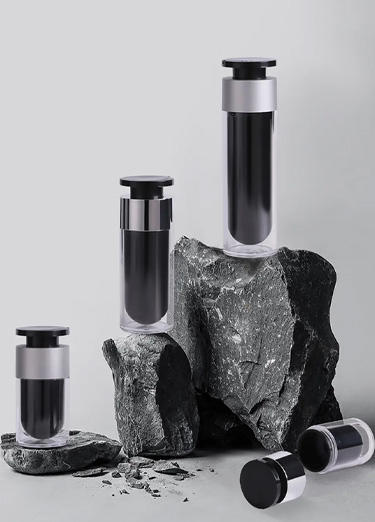
Deodorant stick containers are special containers used to store and apply deodorant sticks, and their material and manufacturing process are crucial for product protection and user experience.
Material Selection
Plastic Containers:
Plastic containers are one of the common choices for making deodorant stick containers. Plastic offers advantages such as lightweight, durability, and cost-effectiveness, meeting the needs of most consumers. Common plastic materials include polypropylene (PP), polyethylene (PE), polyvinyl chloride (PVC), etc. They have different characteristics and applications, and can be selected and used according to product positioning and market demand.
Glass Containers:
Glass containers are commonly used for high-end and delicate deodorant stick products. Glass materials have high transparency, good texture, and easy cleaning, showcasing the high quality and exquisite appearance of the products. Although glass containers are relatively heavy and fragile, their high quality and aesthetic appeal attract a certain segment of consumers.
Metal Containers:
Metal containers are also used in some luxurious and high-end deodorant stick products. Stainless steel, aluminum alloy, and other metal materials have good corrosion resistance and thermal insulation properties, protecting the products from external environmental influences. Attention needs to be paid to processing technology and anti-rust treatment during the production of metal containers to ensure product quality and durability.
Manufacturing Process
Injection Molding:
Plastic containers usually adopt injection molding technology. This process involves injecting molten plastic material into a mold and solidifying it through cooling. Injection molding technology offers advantages such as high production efficiency and low cost, suitable for large-scale production and rapid delivery to the market.
Blow Molding:
For some plastic containers with complex shapes or hollow structures, blow molding technology is often used. Blow molding involves blowing molten plastic material into a mold to achieve hollow and irregular-shaped plastic container production. This process requires precise molds and operational techniques but can produce high-quality plastic containers.
Glass Forming:
Glass containers are typically made using glass forming processes, including molding and blowing methods. These processes require high temperature and pressure conditions, demanding advanced equipment and operational skills but can produce high-quality and aesthetically pleasing glass containers.
Metal Processing:
Metal container production mainly involves processes such as stamping, stretching, and welding. These processes require metal material processing and treatment, as well as the use of molds for shaping. Metal containers often require rust prevention treatment and surface finishing to improve product quality and appearance.
Leave a Reply
Your email address will not be published.Required fields are marked