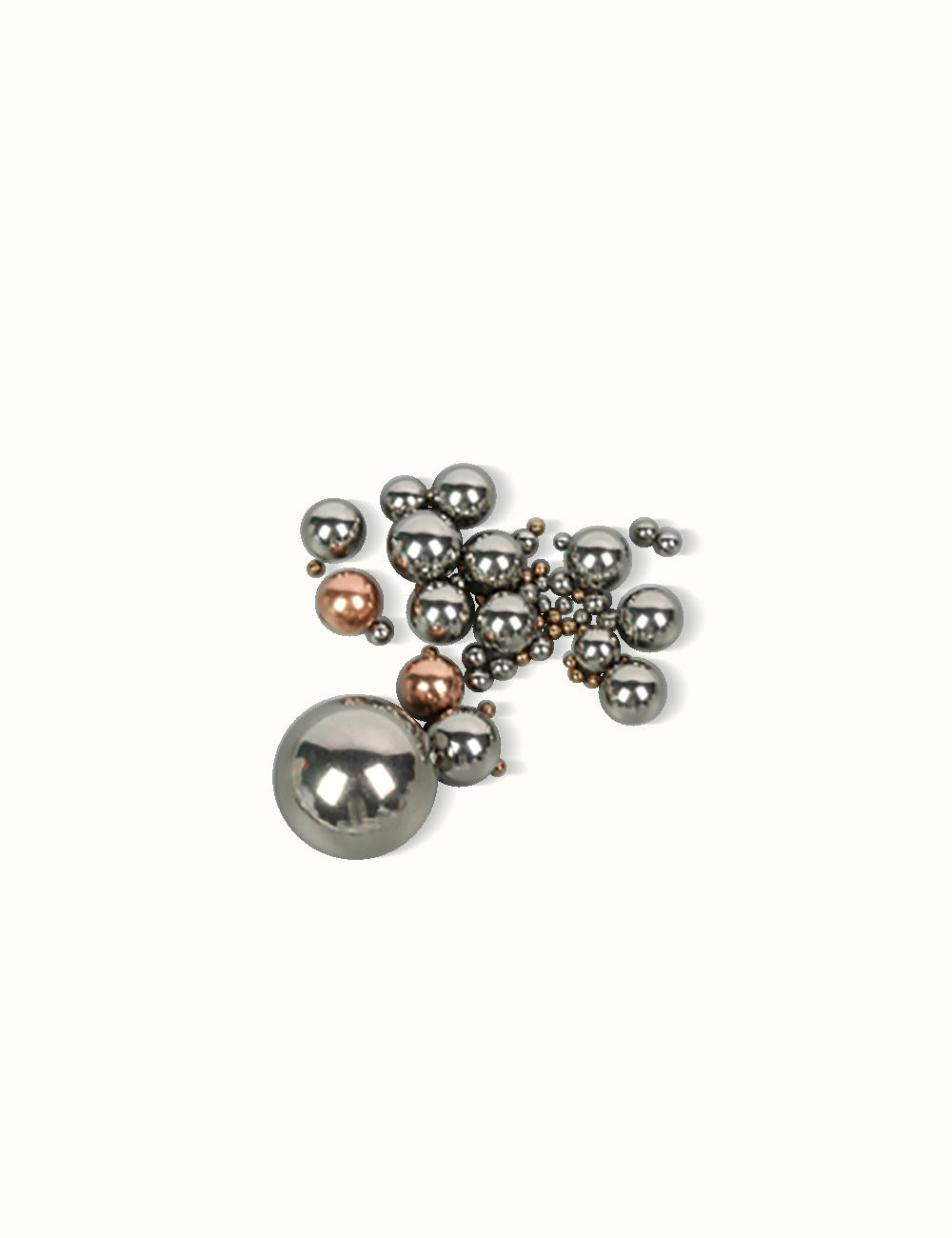
Surface Roughness: The roughness of a surface finish plays a pivotal role in determining the frictional properties of plastic roller balls. A smoother surface minimizes the microscopic peaks and valleys that contribute to friction, resulting in lower resistance when the roller ball is in motion. This reduction in friction can lead to enhanced speed and efficiency in applications such as bearings, where low friction is essential for optimal performance. Conversely, a rougher surface can increase friction, leading to higher energy consumption, potential overheating, and accelerated wear. Therefore, the selection of the appropriate surface roughness is crucial for balancing performance and durability in specific applications.
Material Properties: Different plastics exhibit varying inherent properties that affect their surface characteristics. For instance, high-performance plastics like polyether ether ketone (PEEK) or polyamide (Nylon) may offer enhanced wear resistance and lower friction coefficients compared to standard plastics. These properties can be influenced by the surface finish, where finer finishes often allow for better lubrication retention. This characteristic is particularly important in applications where the roller balls are subjected to continuous motion, as effective lubrication can mitigate wear and extend service life.
Coatings and Treatments: The application of surface coatings or treatments can significantly enhance the performance of plastic roller balls. Coatings such as polytetrafluoroethylene (PTFE) or specialized lubricants can create a low-friction surface, substantially reducing wear over time. These treatments can also offer additional protective benefits, safeguarding the roller balls against environmental factors such as moisture, dust, or corrosive agents that could otherwise compromise the surface integrity. The choice of coating is often dictated by the specific operating conditions, including temperature ranges and load capacities, ensuring that the roller balls maintain optimal performance throughout their lifespan.
Contact Surface Compatibility: The interaction between the surface finish of the roller ball and the surface it contacts is a critical consideration. An incompatible finish can lead to increased wear and potential operational failures. For example, if a plastic roller ball with a smooth finish is used on a highly textured surface, the mismatch may cause excessive localized wear, resulting in decreased efficiency and potential damage to both the roller ball and the mating surface. Therefore, understanding the tribological interactions and selecting finishes that complement the operational surfaces is essential for optimizing performance.
Temperature Resistance: The thermal properties of surface finishes can significantly influence the performance of plastic roller balls under varying operational conditions. Certain finishes are designed to withstand temperature fluctuations without degrading, which is critical in applications involving high-speed rotation or heavy loads. For instance, a finish that retains its integrity at elevated temperatures can help maintain stable friction characteristics, preventing overheating and premature wear. Enhanced temperature resistance can improve the roller ball’s overall reliability and safety in demanding environments.
Wear Resistance: The durability of plastic roller balls is closely linked to their surface finish. A well-executed surface finish can enhance wear resistance by creating a dense, uniform surface that withstands repetitive loading and movement. This characteristic is particularly crucial in high-frequency or high-load applications where traditional wear mechanisms may lead to rapid degradation. By minimizing the rate of wear, the roller balls can maintain their shape and performance, thereby reducing the need for frequent replacements and associated maintenance costs.
Stainless steel ball for roll on bottles
Leave a Reply
Your email address will not be published.Required fields are marked