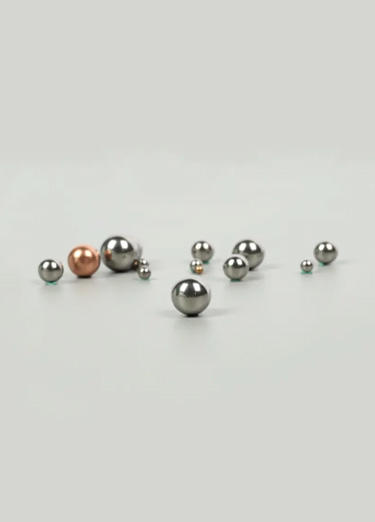
Moisture Resistance: Plastic roller balls, particularly those manufactured from engineering-grade polymers like nylon, acetal, or polyethylene, exhibit excellent moisture resistance, making them a suitable choice for applications where exposure to water or humidity is common. Unlike metal roller balls, which are prone to corrosion, plastic materials inherently resist rust and oxidation. This characteristic ensures long-term reliability in wet environments. However, depending on the plastic type, prolonged or repeated exposure to high levels of moisture can cause minor material expansion or swelling, potentially affecting the rolling precision. To mitigate this, high-performance plastics with low water absorption rates are recommended for environments with constant moisture exposure.
Dust and Contaminant Exposure: In environments with heavy dust or contaminants, plastic roller balls tend to offer better performance than their metal counterparts, especially when compared to lubricated metal balls that can attract dust and debris. Plastic's non-lubricated surface reduces the likelihood of particulate matter sticking to the ball, allowing for smoother operation. However, in highly contaminated settings, dust and debris may still accumulate around the ball or within the bearing housing, leading to friction, restricted movement, or gradual wear over time. To maintain optimal performance in dusty environments, protective features such as seals or shields can be integrated into the ball housing, preventing contaminants from entering the rolling mechanism. Regular cleaning and maintenance can also extend the life and ensure smooth functionality.
Self-Lubricating Properties: Certain plastics, such as PTFE (Teflon), UHMW (Ultra-High-Molecular-Weight Polyethylene), and some grades of nylon, possess self-lubricating properties. This feature is highly beneficial in environments with contaminants or debris, as it reduces the need for external lubrication, which could otherwise attract dust or other particulates. The self-lubricating nature of these plastics minimizes friction during operation, promoting smooth movement even in the presence of external contaminants. Moreover, these materials tend to wear more evenly, ensuring longer-lasting performance in industrial or harsh environmental conditions. For users seeking minimal maintenance, self-lubricating plastic roller balls are an optimal choice, especially in settings where regular lubrication may not be feasible.
Durability and Wear Resistance: While plastic roller balls are typically less prone to corrosion and chemical degradation than metal or ceramic balls, their relative softness makes them more susceptible to wear when exposed to abrasive contaminants. In environments where sharp or hard particles are present, such as in mining, construction, or heavy industrial settings, the plastic material may experience faster wear compared to harder materials like stainless steel or ceramics. However, advancements in polymer technology have led to the development of high-strength, wear-resistant plastics designed to withstand abrasive conditions. These materials, often reinforced with additives like glass fibers or carbon, can significantly enhance the ball’s resistance to wear while maintaining the benefits of corrosion and moisture resistance.
Stainless steel ball for roll on bottles
Leave a Reply
Your email address will not be published.Required fields are marked